By Larissa Donovan, Minnesota Reformer
The following story is the first in a series produced in a collaboration between Energy News Network and KAXE/KBXE.
World leaders in Dubai recently concluded the latest United Nations conference on climate change, where experts and advocates repeated urgent pleas for governments to phase out fossil fuels and transition to clean energy.
In Minnesota, that change is underway. A new state law requires power companies to only sell clean electricity by 2040. Electric vehicle sales are growing, and energy efficient heat pumps are starting to replace gas furnaces — even in northern Minnesota.
But one of the biggest challenges for eliminating greenhouse gas emissions in Minnesota will be finding clean energy solutions for one of the state’s signature industries: taconite mining. The state’s Iron Range supplies three-quarters of the raw material used to make domestic steel. Getting it out of the ground requires massive, diesel-powered trucks and other heavy-duty equipment for which less-polluting options aren’t yet widely available.
The steelmaking industry is facing pressure from customers and governments to reduce its climate impact, and Minnesota mine operators Cleveland-Cliffs and U.S. Steel are both exploring new fuels and technologies to help them meet sustainability goals.
According to the companies’ public statements to shareholders, the path forward is likely to include investments in new, more efficient vehicles and equipment, along with a switch to powering them with renewable electricity, biogas, or hydrogen instead of coal or gas.
U.S. Steel announced in April 2021 a goal to achieve net-zero carbon emissions by 2050. Cleveland-Cliffs says it’s already exceeded its goal of reducing greenhouse gas emissions 25% by 2030.
The transition to clean energy could create new economic opportunities for the Iron Range, experts say, including the possibility to process iron ore on-site into a cleaner, premium product.
A recent event hosted by the city of Duluth and the National Renewable Energy Lab called industrial decarbonization the “billion-dollar question for the Northland.” Rolf Weberg, leader of the University of Minnesota-Duluth’s Natural Resources Research Institute, says industrial operations have a real interest in reducing their carbon footprints.
“When you look globally between steel and concrete, that accounts for between 16-18% of carbon dioxide emissions globally,” Weberg explained. “Countries and industries are really trying to reduce their carbon footprint because we’re not meeting carbon goals across the globe.”
Weberg said NREL is interested in Minnesota because of its resources. Hydrogen, for example, is a clean-burning fuel that can be produced with no emissions using water and renewable energy – both relatively plentiful in Minnesota.
“(This includes) infrastructure for future energy, access to water — all of the things you need to have a hydrogen-based approach to preparing green iron and steel,” he said.
Aaron Brown, a Hibbing native and columnist who has written extensively about the region’s culture and economy, says the Iron Range is in a unique position to capitalize on new technologies and production methods designed to eliminate climate emissions. For example, one strategy steelmakers are exploring involves processing higher-grade iron pellets in electric arc furnaces, which is less geographically constrained by access to coal.
“What the new technology might do is create opportunities for entrepreneurs, and existing companies like Cleveland-Cliffs or U.S. Steel, to produce (steel) in Minnesota,” Brown said in a phone interview. “Now, whether that will happen or not, of course, is subject to speculation, but it is an opportunity to open up modern industry near the mouth of iron mines. And that should be very interesting to people in northern Minnesota.”
On the Range
Minnesota’s Iron Range has experienced monumental shifts since settlers found iron-rich deposits there in the late 19th century. The giants of American industry — James J. Hill, Andrew Carnegie and John D. Rockefeller — collectively created U.S. Steel, the world’s first billion-dollar company, with iron ore largely mined from the Iron Range.
Taconite is a hard, dense rock containing a mixture of silicates and magnetite. After it’s mined in vast open pits, it is crushed into a fine powder, with the magnetite extracted to eventually create marble-sized pellets that contain over 65% iron.
Mining efforts in the Mesabi Iron Range have focused on taconite ore, a lower-grade iron ore processed from vast pits, since the 1950s. Taconite mining transformed the region after underground mining depleted the high-grade hematite deposits. Forty million tons of iron ore are mined there each year.
That ore from Minnesota is shipped across the Great Lakes to plants from Chicago to Pittsburgh, where it is combined with coke — a product derived from coal that is shipped by rail from Appalachia — to make steel.
But what if coal were taken out of this equation? New shifts in technology are moving toward using specially formulated iron briquettes in electric arc furnaces instead of lower-grade iron materials in coal-powered blast furnaces. And Iron Range taconite plant owners Cleveland-Cliffs and U.S. Steel are both increasing production of a new type of iron pellet that does not require coal-powered blast furnaces to process into steel. Electricity can be used instead, meaning a rail connection to coal mines may no longer be necessary for processing the raw material into steel.
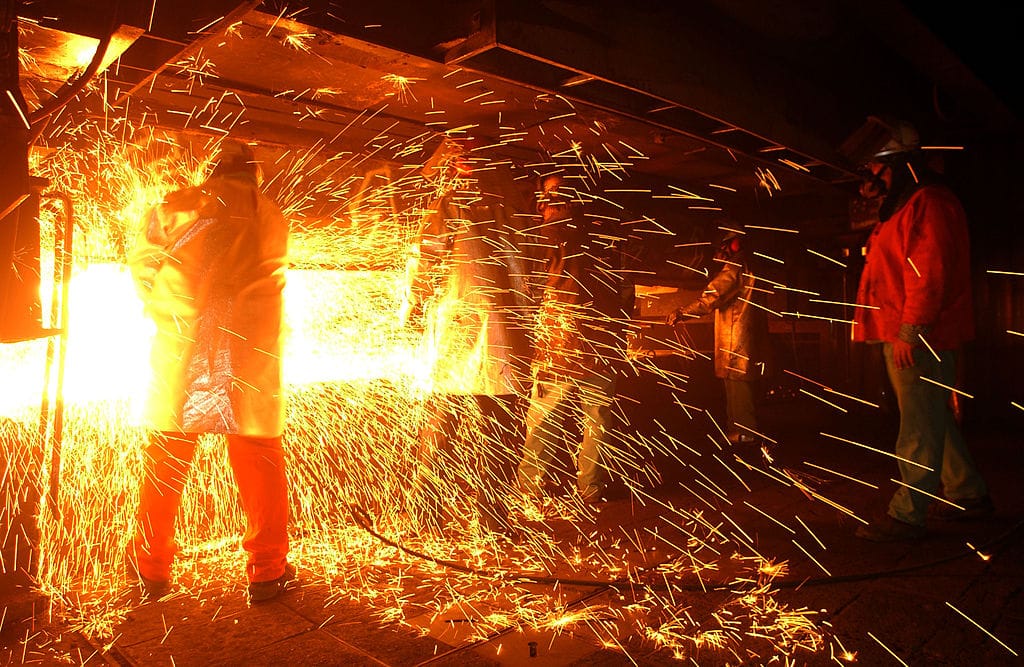
These direct reduced-grade pellets are a metallic iron product instead of an iron oxide product like taconite. And they require less energy to process. The company did not respond to interview requests, but its website lists the environmental benefits of these pellets.
“If we converted United Taconite’s full standard pellet production … net greenhouse gas emissions would decrease by approximately 370,000 tons per year,” Cleveland-Cliffs states.
U.S. Steel announced in 2022 plans to break ground on a new $150 million direct reduced iron production facility near Keewatin on the Range. In November 2022, the company announced Keetac was the selected site for the expanded operation. Keetac currently employs about 400 people.
“Keetac’s high quality ore body and long mine life makes it the best choice for DR-grade pellet capabilities. We will have the ability to produce both blast furnace and DR-grade pellets at Keetac in the future. These actions will allow us to become increasingly self-sufficient to feed our mini mills segment with key metallics.”
Steel, without the fossil fuels
Weberg defines “green” iron and steel as having no fossil fuels involved at any point in its production.
“Our iron industry in Minnesota has been working toward this for some time,” Weberg said. “Our colleagues at Cleveland-Cliffs and at U.S. Steel have been making significant progress with direct reduced grade pellets.”
Brown speculated about a possible future with steel created using hydrogen power and what that could mean for the Iron Range.
“What hydrogen steel might do for Minnesota is create the opportunity … for efficient and profitable steel production near where the mining occurs — an opportunity that doesn’t exist now because the cost of getting the coke and coal … to Minnesota is prohibitive,” Brown said.
As in decades before, the ebbs and flows of the global steel market will continue to impact the Iron Range. As policymakers and manufacturers look toward a sustainable future, the Iron Range may be well poised to prosper in a new, green economy built on the industrious foundation of its core: mining.
This article first appeared on Energy News Network and is republished here under a Creative Commons license.
Minnesota Reformer is part of States Newsroom, a network of news bureaus supported by grants and a coalition of donors as a 501c(3) public charity. Minnesota Reformer maintains editorial independence. Contact Editor Patrick Coolican for questions: info@minnesotareformer.com. Follow Minnesota Reformer on Facebook and Twitter.